Serviceability Requirements as Service CAD Geometry
Deployed via CADPDM, USE* Automotive’s methods for Swept Service Volumes have proved their worth in many environments and contexts as a simple and failsafe way to represent critical aspects of serviceability requirements to the entire collaborative engineering community.
Ian Smith, Operations Manager, USE* Automotive
Digital serviceability support from USE* Automotive promotes and enculturates a design for serviceability mindset into product development activities. USE* classify these services as SERP (Service Evaluation and Repair Process), reflecting both the competent expertise that we provide
to support this function and our out of the box process toolset that we can deploy and adapt to any of our customers’ product development PLM systems.
Swept Service Volumes are a critical aspect of this process, acting as sleeping ambassadors for the serviceability message embedded in the CADPDM package arena.
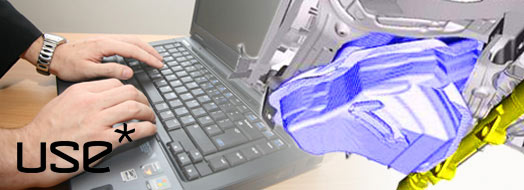
The Challenge
Service access and withdrawal strategies for a priority component are dependant on the vehicle package as a whole.
For example, the design and package of an alternator assembly must ensure that the retaining bolts and electrical harness connections are orientated in a way that it is possible to access by hand, and with a standard workshop tool, from either above or below the engine bay, or via the wheel arch.
While these considerations will be discussed between the engineer responsible for the alternator and the service engineers responsible for the service strategy, delivery of the actual comprehensive service solution is not limited to just these two individuals. This is because any access strategy relies on all of the surrounding components being designed and packaged with this same strategy in mind. For example, if it is decided that an access strategy from beneath the engine bay is preferable, then the routing of a solid air conditioning pipe below the alternator can individually render the service access strategy unfeasible without the air conditioning engineer necessarily being aware of the issue or requirement.
If the emphasis could be placed with component engineers to investigate and resolve a potential service issue that could arise as a result of their package or design proposal, then there would be an increased opportunity for these issues to be resolved before a design progresses to a sufficient level of maturity that renders a service driven design change harder to justify.
The Solution
USE* Automotive have proposed a range of solutions to this problem in various forums with our customers. For example, in the future CADPDM solutions may allow for the representation of engineering requirements graphically in a package, associated with both geometry for parts and systems, and with space around a part or system critical for reasons of avoided temperature transfer, access during the build process, or for disassembly and reassembly access in service.
In lieu of these types of IT architectural solutions becoming available, USE* set about an effective means of realising the need to conclusively communicate an access requirement within a vehicle package. It quickly became apparent that, combined with frequent and clear communication between service and product development representative, a method of providing the engineering community with a graphical geometric representation of service access space - a Service Swept Volume - would be the best approach.
A Service Swept Volume (SSV) is a geometrical representation of a service strategy. The SSV can be published to the engineering PDM database (for example, TeamCentre Engineering) for a particular vehicle programme, making it available and visible to the entire vehicle engineering team. Predominantly a SSV will be produced to represent the withdrawal path taken by a component when it is removed for service. SSVs are used to protect critical components to ensure that they are easily removed and replaced without unnecessary level of disassembly. They are designed to alert both component and package engineers to those service requirements in the vehicle which would not be obvious from looking at the components modelled in their nominal positions. In addition to SSVs for service withdrawal paths, geometric representation of tool and technician hand access can also be created and published.
USE* Automotive’s SERP methodology identifies ranges of parts and systems for which SSV representation in vehicle package is important. It also identifies the optimum times for this data to be introduced into the mix, complementing the progress of the evolving vehicle layout and package. Publication of service requirements associated with the SSV can also be integrated into this approach, and routine updates of SSV data (in alignment with the evolving package and service strategy intent, and based on routine liaison with product development engineers) is also important.
To represent a service withdrawal path, a SSV is created first by solving the path using a path planning software programme (such as Kineo Path Planner). By importing a target component and the surrounding package environment, the path planning engine can solve a clash free path that allows the target component to be moved from its starting position to a specified end point (in most cases this is position away from the vehicle). When a path is successfully solved, a geometric motion file can be exported to generate a solid volume. Creation of the final Swept Volume geometry is achieved using CAD, depending on the complexity of the path. A SSV can also represent the required sweep of a wrench or ratchet when positioned on a fastener, and can also be created to represent fluid fill and drain paths.
Along with servicing as a visual reminder and basis for dialogue between serviceability experts and product developers, SSVs are integrated into holistic clash detection processes conducted routinely to verify evolving system compatibility.
Its Benefits
SSVs, as something approaching visual representations of service requirements, and as an aspect of a wider range of USE* Automotive supporting measures and processes, have proved to be a competently successful measure wherever implemented.
Value for money is delivered to the customer de facto, because their inclusion in the vehicle package prevents oversights emerging in the developing package that will cost money to rectify later in the design cycle or even in the aftermarket. If properly supported by comprehensive SERP and service engineering processes and tools, SSVs fulfil an ambassadorial role for serviceable design, advertising a service message which becomes a subject for discussion in forums such as clash results analyses and package meetings.
SSVs can also play a critical role in automated clash detection processes, where they serve to alert the vehicle management team of clashes between product and service CAD geometry. This will be policed to a resolution with SERP and engineering teams held to account at critical design gateways, and effectively means that SSVs cannot be selectively ignored by engineering teams.
An additional benefit realised from the creation of SSVs within the service engineering team is the clash validation of the path planning-generated CAD SSV to ensure that critical parts were not omitted from the original solve environment.
Our Achievements
Specific examples of design changes to improve serviceability driven by SSVs are manifold. One examples includes capturing the implications of a late change re-routing of solidly mounted air conditioning lines in an engine bay (which would otherwise have prevented the removal of critical emissions system components). In this case SERP engineers were alerted to the late change via the clash detection process and were able to engage with the climate control team. This led to a new package that facilitated the removal of the emissions components without breaking into the air conditioning system. Another instance (using a drain path SSV in clash detection) delivered design changes to a front subframe that would have collected engine oil as it was drained from the sump.
Perhaps the most important achievement of the USE* Automotive team with respect to SSVs and the benefits they deliver to our customers, is not the simple fact of SSV creation in its own right, but the development of a process toolset that supports this activity. This toolset transforms an idea into a comprehensive and robust system that ensures dependable and consistent support for a complete vehicle programme from early concept design through to engineering completion. This value and dependability, as a part of USE* Automotive’s SERP process toolset, composes a key element of a valuable methodology that can be deployed with consistent results to any USE* customer.
Case Studies
Case Studies
SERP for fleet vehicles
USE* support for the commercial arena
USE* in Concept Design
‘Design for service’ on carry-over technology
XF Residuals
The USE* contribution to the XF's world class ...
'Design for Service'
‘Design for service’ with USE*